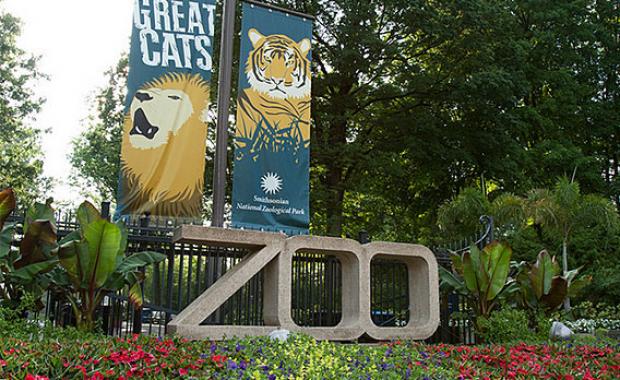
Meltech recently completed the Smithsonian Institution National Zoo Park Renovations to the Smithsonian Conservation Biology Institute Animal Building 1 Bio-Repository located in Front Royal, Virginia with great success. Meltech completed this project on time and within budget for the Smithsonian Institution.
The project contract officer had to say this, “THANK YOU ALL for being part of the Great Team that worked together to achieve a project that we are all very proud of.” – Marc. M. Muller, Resident Engineer – Smithsonian Operations – Office of Projects, Design and Construction National Zoological Park & Conservation Biology Institute
This work for the Building 1 Bio-Repository renovation included but was not limited to:
- The renovation/partial demolition, and one-story “hyphen” addition allows for adaptive reuse of existing Building 1 for a cryogenic laboratory and bio-repository.
- Planned salvage of existing steel roof trusses and clay roof tiles.
- Demolish existing connector between Buildings 1 and 2 and replace with new larger “hy-phen” connector with support spaces.
- Opportunity for high-performance components that demonstrate sustainability (rain gar-dens, salvaged and recycled building materials, energy-saving equipment and fixtures).
- Electrical Work – installed a 500kva 13,200 volt primary to 120/208 volt pad mounted transformer, this feeds a 1200-amp main switchboard by a 4×6”conduit concrete incased ductbank. The building has a 300kva backup generator with a 300kw load bank, and a 1200-amp manual transfer switch to add a portable generator to the system if needed. The generator system connects to the building by a 8 x 6” conduit concrete incased ductbank feeding a 1200-amp switchboard. These two switchboards feed three closed transition automatic transfer switches to provide normal and backup power to most of the building load.
The project included the following divisional activities:
DEMOLTION work for the project included the demolition of cages and block walls, roof tile and roof deck, interior slab hyphen and remainder of the site work.
SITE WORK for the project included 2 retaining walls; one at Building 2 and another at the rear hyphen entry. Site work included concrete knee walls and concrete sidewalks the courtyard to include stone facing and capping at the knee walls. The remaining site work included asphalt paving, concrete pavings, landscaping, site stabilization and removal of E&S controls.
SITE UTILITY work included the water and fire mains, service duct banks, generator duct banks, sanitary sewer. The site utility work included the site concrete utility pads, set transformer, generator and ATS. The site utility work also included the courtyard excavation, courtyard storm sewer, courtyard BMP’s and the site lighting.
HYPHEN. The Hyphen work included the layout for the Hyphen, Exposing the Building 2 foundation, survey of the existing conditions, design and construction of the underpinning.
FOUNDATION The foundation work included the excavation, layout, excavation, form, rebar and placement of the footings. The additional foundation work the underslab for the plumbing and electrical rough-in. The final foundation work included the forming, stone, rebar and placement of the SOG.
STRUCTURE The structural work included the masonry of the exterior walls, setting of the bar joists, installation of the steel decking and pour stop. The structural work included the rough-in, rebar and placement of the roof deck concrete, the masonry of the interior walls and knee walls. The structural work also included the temporary Dry In the mechanical and electrical rooms. The final structural work included the setting of the screen wall steel frames and the SBS membrane roof.
MECHANICAL The mechanical work included setting of the boilers, installation of the AHU-1, CRAC unit and ductwork. The mechanical work included the setting of the chiller, piping and setting and control wiring of the mechanical equipment and duct air leakage test. The mechanical work also included the piping of the plumbing equipment, setting of sprinkler equipment, electrical connections to equipment, insulation of ductwork, installation of sprinkler piping, pressure test of the plumbing and mechanical piping and the insulation of plumbing and mechanical piping.
ELECTRICAL The electrical work included the installation of the security equipment and panel, fire alarm equipment and panel and telecommunications and data equipment and panel. The electrical work also included the installation of the switchgear and panelboards and the pulling and termination of wires and permanent power connections.
ROOF STRUCTURE The roof structural work included new nailers, new hip ridge beams, steel deck, steel and setting for cupola, insulation, ice and water shield, removal and installation of roof tile and lighting protection.
SLAB The slab work included the removal of excess dirt in the middle, underslab rough in, form, stone and rebar and placement of concrete.
EXTERIOR SKIN The exterior skin work included the infill of opening with masonry or DW, air barrier, mineral wool and clips, vertical Z girts and sheathing, exterior stucco, soffit furring and framing, exterior windows, cement board fascia/soffit, installation of louvers, installation of fixed louver equipment screen, installation of formed metal wall panels, installation of overhead coiling door, installation of auto sliding doors and gutters and downspouts.
INTERIOR BUILDOUT The interior buildout work consisted of the rough in electrical in walls, layout of the partitions, installation of the main duct trunk lines, framing of the walls and setting of the door frames. The interior buildout work included the rough-in of mechanical and plumbing above the ceilings, wall close in inspections, insulation, hanging and finishing of drywall, installation of fume hood, painting of exposed decks, priming, painting and point up. The interior building work also included ceramic tiling, interior glazing and installation of wire mold, ceiling grids and toilet partitions/access/FECs. The interior work included the installation of signage, completion of ceiling rough in, installation of plumbing fixtures, close in of ceiling inspections, drop ceiling tile, linoleum flooring and base, resinous flooring, air balance. The final interior buildout work included the installation of the lab casework, doors & hardware and mobile shelving and MEP connections to the casework and MED glasses.
Leave a Reply